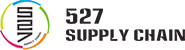

Since the official commercial use last year, the application of 5G technology has become a hot topic.
By the end of July 2020, China had opened more than 460,000 5G base stations, and plans to open more than 600,000 by the end of 2020, covering cities at and above the prefecture level. Behind the laying of infrastructure, the huge 5G application scenario has emerged, with industrial Internet bearing the brunt.
Yin Hao, an academician at the Chinese Academy of Sciences, previously said that human society is entering a smart era of the Internet of everything, and the industrial Internet will trigger a huge change in the manufacturing model. The scale of China's industrial Internet industry reached 2.13 trillion yuan in 2019 and is expected to exceed 5 trillion yuan in 2025.
"At present, the application of 5G in the manufacturing industry has formed certain typical industrial application scenarios, including 5G+ remote operation and maintenance, 5G+ industrial control, 5G+ warehousing and logistics." Recently, in the "2020 China Intelligent Manufacturing Industry Annual Conference" hosted by the 21st Century Business Herald, Dong Kai, vice president of CCID Consulting Co., Ltd. released the "2020 China's new infrastructure Industry track and investment value Research White Paper", "5G+ industrial Internet" listed the first five core tracks.
As the "aggregator" of 5G technology in the field of industrial manufacturing, the development of 5G digital factory also attracts people's attention. As the 5G application of many enterprises, including Lenovo Group, has entered the substantive stage, the development of China's 5G factories is heading for a new journey.
5G reshapes smart factories
The industry has been exploring intelligent manufacturing for some time. As early as Hannover Messe 2013, the concept of Industry 4.0 was introduced. Subsequently, the great wave of reform around industry 4.0 swept the global manufacturing industry.
In fact, after the first three industrial revolutions, the fourth Industrial Revolution, based on the Information Physical Convergence system (CPS) and marked by highly digitized, networked, machine self-organization of production, with the introduction of the Internet of Things and services, enables companies to build global networks to integrate their machines, storage systems, and production facilities.
Thus, "intelligent manufacturing" began to enter people's vision, and correspondingly, smart factories became the core of this revolution. In fact, the essence of intelligent manufacturing is to provide conditions for intelligent production through intelligent production system and networked distributed production facilities.
However, the development of intelligent manufacturing faces many challenges. For example, how to realize the safe and reliable connectivity of the whole factors of production, the whole industrial chain and the whole value chain, and how to realize the network coordination of people, machines and things oriented to industrial production and service systems still need to be solved.
The addition of 5G technology will bring new imagination to intelligent manufacturing. "Maybe 80 percent of the future use of 5G will be in manufacturing," Dong said. He said that the important appeal of the manufacturing industry lies in the detection of parts, which is a large integrated device, requiring wireless communication technology, ultra-high definition video, etc., and all these can be met by 5G technology at present. "After some industrial manufacturing enterprises integrate 5G modules, there is a great opportunity to open a new blue ocean in the industrial control layer."
IDC China senior research manager Cui Kai further pointed out that the current traditional manufacturing industry more stay in the automation stage, the application of 5G new technology is expected to leapfrog the digital, networking stage, so that the industry to the intelligent scene.
"While traditional intelligent factories are more likely to use wired or Wifi networks for data transmission, 5G networks can really achieve stable wireless transmission and provide more flexibility for production," Cui Kai analyzed, "At the same time, a big advantage of 5G is the high bandwidth rate of the upstream and downstream. In industrial manufacturing, whether it is machine vision for product quality detection, or robot control and operation, there are strict requirements for bandwidth."
At the same time, Cui said 5G technology can natively support edge computing and transform large bandwidth or traffic services from being centered in data centers to being deployed at edge terminals, thus greatly reducing latency and response speed.
Pan Helin, executive director of the Institute of Digital Economy at Zhongnan University of Economics and Law and author of 5G New Industry, stressed that the three application scenarios of 5G fully fit the future construction direction of smart factories.
"The features of 5G, such as high speed, low latency and large connectivity, are satisfying the construction of smart factories. The biggest change is in flexible production, which becomes more adaptable and enables enterprises to better respond to the market." "On the other hand, smart factories can significantly reduce labor costs and achieve an overall improvement in product processes, leading to a higher level of product standardization and higher yield," said Pan.
Explore the 5G factory
As an important investment track in the future, domestic manufacturers have also set their sights on 5G+ industrial Internet and started to practice 5G factories.
According to incomplete statistics, at present in China, many manufacturing enterprises including Lenovo Group, Comac, Haier Group, Sany Heavy Industry, Valing Hunan Steel, Tianjin Port, China Southern Power Grid and so on have carried out 5G application exploration. The vertical application scenarios of 5G factories have covered the fields of aviation, 3C household appliances, machinery manufacturing, steel, ports and other "major countries".
In this process, operators, communication equipment and service providers, as well as related hardware and system manufacturers are actively promoting technologies and solutions related to 5G factories.
For example, Lenovo Group has long started to lay out its strategic development direction of intelligent reform, and has made a comprehensive layout in the core layer of "new infrastructure" with its unique "end-edge - cloud - network - intelligence" architecture to provide a comprehensive solution for the realization of digital and intelligent infrastructure, namely "intelligent infrastructure".
At the same time, the three major carriers are also ramping up their 5G capabilities. For example, China Mobile has joined hands with Ericsson to carry out the 5G smart factory transformation and application pilot. Jiangsu Mobile provides the network environment and Ericsson Nanjing factory serves as the transformation object. The smart factory solution covers four scenarios: equipment detection management, environmental monitoring management, material supply management and personnel operation and interaction. There are 7 specific application solutions including smart screwdriver.
In terms of mode, most of the current construction of 5G plants is carried out jointly by operators, equipment manufacturers and manufacturers. In this process, the close cooperation of all parties becomes the premise and key to the implementation of technology. A number of industry insiders bluntly say that the current promotion of 5G is more about operators holding 5G network to find application scenarios. Considering the high cost of network construction and operation and maintenance in the early stage of 5G promotion, it is of little significance to simply build 5G network and solve the demand for information transmission. What needs to be explored more is to explore application modes such as intelligent management and control on the basis of transmission.
"The whole 5G factory is indeed full of scenarios and pilot projects, but whether it can really solve the industry's pain points still needs a deep combination of industry knowledge, background and technology." Cui Kai analysis said.
Compared with other manufacturers, Lenovo Group is out of its own 5G factory path. In the middle of June this year, the industry's first 5G IoT automated assembly line "Quantum line" was officially put into production in Lenovo's Wuhan base. All the equipment of the entire production line are collected and distributed to the entire background system through sensors and 5G technology, so that the staff can know the operation status of the entire production line even remotely in the background. In addition, in September, the "Mercury Line" and "Nezha Line" were officially opened in Lenovo's Lianbao factory in Hefei and will realize partial application of 5G.
It is important to note that Lenovo's 5G factory truly realizes the "inner loop" of technology. Relying on the 5G private network advantage of Lenovo's own cloud network integration technology, employee operation details and sensor data on automated production lines can be connected in real time. With Lenovo's own hardware provided by the smart device business, each process can be recorded in real time and achieve production traceability.
At the same time, Lenovo's own data center business and Lenovo's Internet of Things and industrial big data business provide stable and reliable storage services for massive production data. The AI technology of quantum wire comes from the capability accumulation of Lenovo Research Institute.
In the view of industry insiders, the application of "internal circulation" in 5G factories, on the one hand, reduces R&D costs, and at the same time strengthens team collaboration, enabling more effective and targeted matching of production around key design nodes and product development. In other words, the complete set of solutions "arranged" by Lenovo itself can better digest the pain points on the production line and form a unique intelligence that fits the production practice.
At the same time, from the data and network level, industrial production lines will be more reliable. "Lenovo's internal network construction is undoubtedly more in line with its own needs, and based on the data, it can make better judgments according to the data," Pan Helin said bluntly. Secondly, this mode can ensure the enterprise's control over the network, and ensure the reliability, security and privacy of the network. To some extent, Lenovo's 5G factory exploration has considerable benchmarking value.
Need to step out of the pilot area
While 5G factories are evolving in full swing, the vast majority of application exploration is still in the "pilot" stage.
"We are currently seeing the launch of 5G in factories. There are not many real large-scale commercial or even direct investment returns. More people are still making some attempts." Cui Kai said.
In his view, the vast majority of current 5G projects are not for profit. "From a normal 5G project, HD cameras are needed in the station, but also with other equipment with computing capacity, a 5G module also needs about 1000 yuan of cost, and then superimposed gateway, 5G base station, the cost of a single station is expected to be several thousand yuan."
For this reason, most companies are still only trying out a small number of 5G production lines. "If the number of stations increases, the cost of traffic transmission costs and computing platform costs in the later period will need to be further calculated." "In the short term, it will be difficult for the deployment of 5G plants to generate quick returns and it will take a certain period of time," Cui said.
In addition, since 5G has just entered commercial use, the market, investment and financing are still in their infancy, and the mobile application ecology, operation support and standard system combined with the new features of 5G are not yet mature. "I think the current 5G development is indeed at an early stage, and the popularity of the network is not high. If we build smart factories, we may have to pay some infrastructure construction costs," "At the same time, an updated iteration of traditional factory and smart factory involves not only equipment, but also data, standards and other aspects. Smart factory may have to work hard to create manufacturing standards in the future."
However, the current layout of 5G production lines is not without large-scale promotion of the "ambition". Lenovo Group is one of them, which has developed the 5G factory model through internal circulation of its own technology. In fact, Lenovo Group has already done a calculation. According to Qi Yue, head of Lenovo's Wuhan manufacturing base, the construction cost of quantum wire totaled 11 million yuan, and the production line is carrying a lot of invisible significance.
According to the introduction of the quantum wire project, the automation rate of its production line jumped 2 times, to 41%, and later will be further increased to 48%. In contrast, the automation rate of traditional assembly lines is only 15 to 20 percent, which reflects the reduction of labor costs.
At the same time, after the application of data analysis and machine vision technology on the basis of 5G, the yield of terminal production has also been improved. Lenovo said, according to internal calculation, every increase in yield of 1 point, about 400,000 yuan can be saved.
According to Lenovo, applications such as 5G and Smart IoT, which are currently being explored within the group, will be replicated first in the Lenovo Southern Intelligent Manufacturing Base, which will be officially put into operation in 2022 with an investment of 2 billion yuan. At the same time, Lenovo continues to export through its own practice. Wang Xiaolan, head of global manufacturing engineering at Lenovo Group, revealed that Lenovo has already carried out cooperation with enterprises such as Comac and Wuhan Petrochemical, to jointly explore the path of intelligent manufacturing transformation.
"How to improve production efficiency, quality and even innovate business models under the background of 5G technology, and enhance the competitiveness of enterprises through technological means, the key is still to deepen the industry and understand the real needs and pain points." Cui Kai stressed, "No matter the enterprise itself to layout, or combined with a third party partner to do, ultimately need to deeply cultivate the industry, even some application scenario integrators, solution providers to do relevant things."